In today’s packaging landscape, plastic containers remain a cornerstone solution for businesses across numerous industries. Their versatility, durability, and cost-effectiveness make them an ideal choice for shipping, storing, and showcasing products. This comprehensive guide explores the world of plastic containers, helping you understand the various types available and how to select the right option for your specific needs.
Understanding Plastic Container Materials
The foundation of any plastic container is the material from which it’s made. Different polymers offer distinct properties that make them suitable for specific applications.
Polyethylene Terephthalate (PET/PETE) – #1
PET is one of the most commonly used plastics for containers worldwide, especially for food and beverages.
Key Properties:
- Excellent clarity and transparency
- Good barrier against gases and moisture
- Lightweight and impact-resistant
- Widely recyclable
PET containers are primarily used for bottled water, soft drinks, cooking oils, and various food products. Their clarity allows consumers to see the contents, while their barrier properties help maintain product freshness. According to industry data, PET accounts for approximately 30% of all plastic packaging produced globally. Container and Packaging
High-Density Polyethylene (HDPE) – #2
HDPE offers exceptional strength-to-density ratio, making it suitable for containers that require durability.
Key Properties:
- Excellent chemical resistance
- Good moisture barrier
- Temperature resistant (-40°F to 180°F)
- Rigid yet lightweight
- Widely recyclable
HDPE containers are commonly used for milk jugs, detergent bottles, shampoo bottles, and industrial chemical packaging. Their superior chemical resistance makes them ideal for housing both food products and non-food items like cleaning solutions. Future Green
Polyvinyl Chloride (PVC) – #3
While less common for food packaging due to potential health concerns, PVC still has specialized applications.
Key Properties:
- Good clarity
- Excellent chemical resistance
- Resistant to oils and fats
- Barrier to oxygen and carbon dioxide
PVC containers are typically used for non-food applications such as household chemicals, personal care products, and medical packaging. Due to health concerns about potential chemical leaching, many manufacturers have moved away from PVC for food contact applications.
Low-Density Polyethylene (LDPE) – #4
LDPE offers excellent flexibility and is commonly used for squeeze bottles and flexible packaging.
Key Properties:
- Highly flexible
- Good moisture barrier
- Chemical resistant
- Impact resistant
- Recyclable (though less widely accepted)
LDPE containers include squeeze bottles for condiments, honey, and personal care products. The material’s flexibility makes it ideal for applications where the container needs to be squeezed to dispense the contents.
Polypropylene (PP) – #5
PP offers excellent heat resistance, making it ideal for hot-fill applications and microwaveable containers.
Key Properties:
- High heat resistance (up to 275°F)
- Good chemical resistance
- Excellent fatigue resistance
- Translucent or opaque appearance
- Widely recyclable
PP containers are commonly used for yogurt cups, margarine tubs, microwaveable meal trays, and medicine bottles. Their heat resistance makes them suitable for hot food applications and microwave use. Earth911
Polystyrene (PS) – #6
PS comes in both rigid and foam forms, with distinct applications for each.
Key Properties:
- Rigid PS: Clear, brittle, good insulation
- Foam PS: Excellent insulation, lightweight
- Low moisture absorption
- Less commonly recycled
PS containers include clear clamshell packaging, yogurt containers, and foam food containers. Environmental concerns have led many municipalities to ban foam PS containers due to recycling challenges.
Other Plastics – #7
This category includes polycarbonate, bioplastics, and other specialized polymers.
Key Properties:
- Varies widely depending on the specific polymer
- Often designed for specialized applications
- May include both petroleum-based and bio-based materials
- Recycling varies by specific material
This category includes containers made from polycarbonate (used for water bottles and food storage containers) and various bioplastics derived from renewable resources.
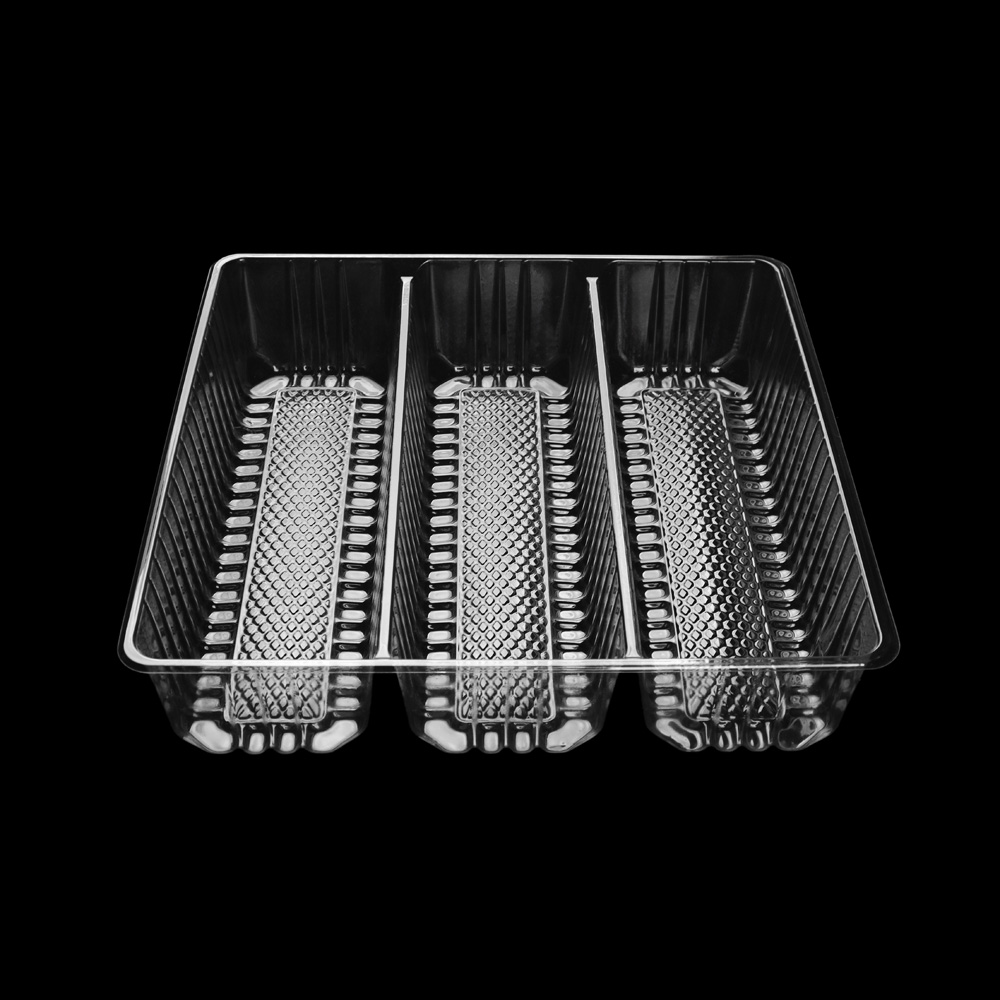
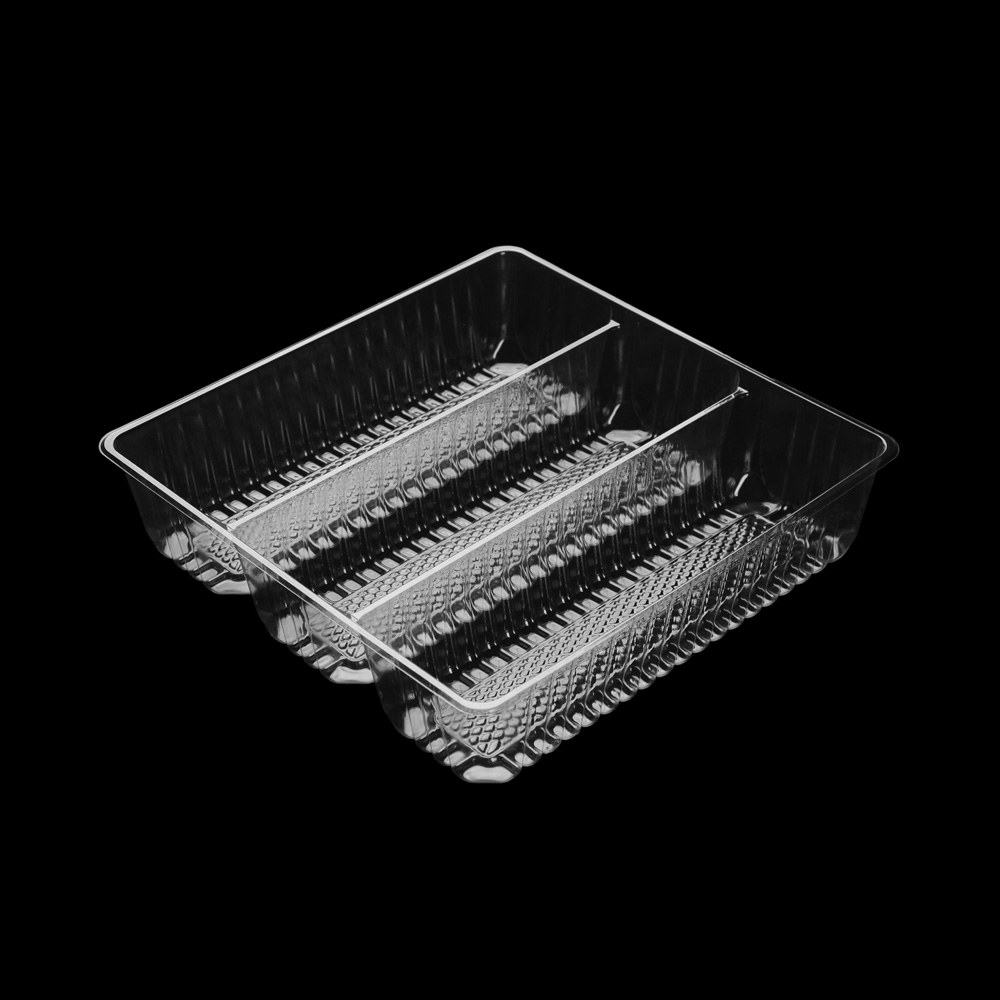
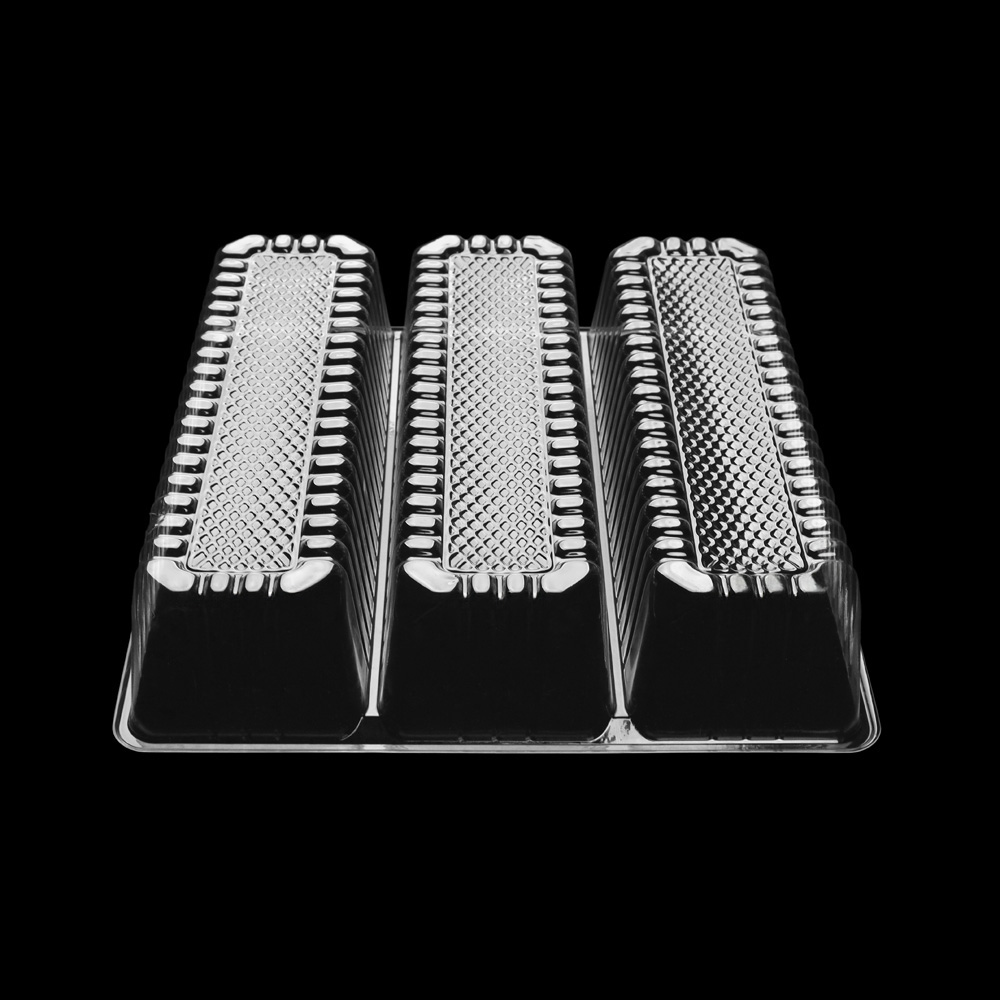

Plastic Container Types by Form and Function
Beyond material composition, plastic containers come in numerous forms designed for specific applications.
Bottles and Jars
Plastic bottles and jars are among the most recognizable container types, featuring:
- Necks and closures: Screw caps, flip tops, pumps, triggers
- Shapes: Round, oval, square, custom
- Sizes: From small samples to large bulk containers
These containers are used for beverages, condiments, pharmaceuticals, personal care products, and household chemicals. Their design often considers not only storage but also dispensing functionality.
Tubs and Cups
Tubs and cups feature wide openings for easy access to contents:
- Designs: Round, square, rectangular
- Closures: Snap-on lids, foil seals, resealable options
- Features: Tamper-evident options, stackable designs
Common applications include yogurt, butter, deli foods, ice cream, and various prepared foods. Their wide-mouth design allows consumers to easily access and scoop contents.
Clamshells and Blister Packs
These containers provide product visibility while offering protection:
- Types: Hinged clamshells, two-piece blisters with card backing
- Features: Product contour, anti-theft design, hanging tabs
- Applications: Electronics, toys, produce, bakery items
Clamshells are popular in retail for their ability to showcase products while providing theft deterrence and physical protection.
Trays and Compartmentalized Containers
These containers feature divided sections for multiple items:
- Designs: Single to multiple compartments
- Features: Stackable, nestable, compatible lidding
- Applications: Prepared meals, produce, medical supplies
Compartmentalized containers are essential for portion control, multi-component meals, and organizing small items.
Bulk Containers and Totes
Large-volume containers for industrial and commercial applications:
- Capacities: From gallons to hundreds of gallons
- Features: Heavy-duty construction, drainage ports, forklift compatible
- Applications: Chemical storage, bulk food ingredients, waste management
These containers support supply chain logistics, waste management, and bulk storage needs in commercial and industrial settings.
Selection Criteria for Plastic Containers
Choosing the right plastic container involves carefully considering several key factors:
Product Compatibility
The container must be compatible with the product it will hold:
- Chemical Compatibility: Will the product react with the plastic?
- Barrier Requirements: Does the product need protection from oxygen, light, or moisture?
- Shelf Life Expectations: How long must the container maintain product integrity?
For food products, FDA food-grade standards must be met to ensure safety and compliance.
Performance Requirements
Containers must perform reliably throughout their lifecycle:
- Temperature Range: Will the product be hot-filled, frozen, or microwaved?
- Impact Resistance: What level of drop protection is needed?
- Stacking Strength: Will containers be stacked during storage or shipping?
- Sealing Performance: What level of leak protection is required?
Testing containers under expected conditions ensures they’ll perform as needed in real-world applications.
Sustainability Considerations
Environmental impact has become a critical selection factor:
- Recyclability: Is the container made from commonly recycled plastic?
- Recycled Content: Does the container incorporate post-consumer recycled material?
- Material Reduction: Is the design optimized to minimize plastic use?
- Alternative Materials: Are bioplastics or biodegradable options suitable?
Many companies now have packaging sustainability goals that influence container selection. EPA Plastics Management
Cost Factors
Economic considerations remain essential:
- Material Costs: Different polymers have different price points
- Tooling Investment: Custom containers require mold development
- Production Volumes: Higher volumes typically mean lower per-unit costs
- Transportation Efficiency: Container weight and nestability affect shipping costs
Finding the right balance between performance and cost is crucial for sustainable business operations.
Brand and Marketing Requirements
Containers increasingly serve as brand ambassadors:
- Transparency: Does the product benefit from being visible?
- Decoration Options: What printing, labeling, or decorating is needed?
- Shelf Presence: How will the container look alongside competitors?
- Consumer Experience: Does the container enhance product use?
The container’s role in brand perception and consumer experience should not be underestimated.
Trends Shaping the Future of Plastic Containers
The plastic container industry continues to evolve in response to market demands and environmental concerns:
Sustainability Innovations
The push for more sustainable packaging is driving significant innovation:
- Lightweighting: Engineering thinner, lighter containers that use less material
- Mono-material Designs: Creating containers with components all made from the same polymer for easier recycling
- PCR Integration: Incorporating post-consumer recycled content into new containers
- Bioplastic Development: Advancing plant-based alternatives to petroleum-based plastics
These innovations help reduce environmental impact while maintaining performance and cost-effectiveness. PlasticsEurope
Smart Packaging Technologies
Technology integration is creating new possibilities for plastic containers:
- NFC/RFID Tags: Enabling digital interaction and authentication
- QR Codes: Providing product information and marketing opportunities
- Time-Temperature Indicators: Monitoring product freshness and safety
- Anti-Counterfeiting Features: Protecting brands from illegal copying
These technologies add value by enhancing product safety, consumer engagement, and supply chain visibility.
Design Evolution
Container design continues to advance to meet changing market needs:
- E-commerce Optimization: Containers specifically designed to survive shipping
- Ergonomic Improvements: Easier-to-hold, pour, and use designs
- Portion Control Features: Built-in measuring and dispensing capabilities
- Multi-functional Designs: Containers that can be repurposed after initial use
These design evolutions enhance consumer convenience while differentiating products in the marketplace.
Regulatory Impact
Evolving regulations around plastic packaging are influencing container development:
- Extended Producer Responsibility (EPR): Manufacturers becoming responsible for end-of-life management
- Plastic Taxes: Fees imposed on non-recycled plastic packaging
- Banned Materials: Restrictions on specific polymers or applications
- Labeling Requirements: Standardized recycling information
Staying ahead of regulatory changes is becoming an essential part of container strategy.
Case Studies: Successful Plastic Container Applications
Food Industry Innovation
A major food manufacturer transitioned from glass to PET containers for its condiment line, resulting in:
- 40% reduction in packaging weight
- 15% decrease in transportation costs
- Zero breakage during shipping
- Maintained product shelf life and quality
The switch also reduced the company’s carbon footprint while preserving brand identity through careful design.
Industrial Packaging Solution
A chemical supplier implemented a custom HDPE container system for hazardous materials:
- UN-rated for dangerous goods transport
- Stackable design maximizing warehouse space
- Integrated handle system for safe handling
- Tamper-evident closure for security
The solution improved safety compliance while reducing handling costs throughout the supply chain.
E-commerce Adaptation
An online retailer developed specialized PP containers for shipping perishable items:
- Thermal insulation properties
- Impact-resistant design
- Leak-proof sealing
- Right-sized to minimize void fill
This solution reduced shipping damage by 85% while maintaining product quality during transit.
Conclusion
Plastic containers continue to provide valuable solutions across numerous industries thanks to their versatility, performance characteristics, and cost-effectiveness. By understanding the different materials, types, and selection criteria, businesses can make informed decisions that balance functional requirements, brand objectives, cost considerations, and sustainability goals.
As the industry evolves, innovations in materials, design, and technology will create new opportunities for plastic containers to meet changing market demands while addressing environmental concerns. Working with experienced suppliers like Reliancepak ensures access to the latest developments and expertise needed to optimize container solutions for specific applications.
Whether you’re looking for standard containers or custom designs, the right plastic packaging can protect your products, enhance your brand, satisfy your customers, and support your sustainability initiatives.